How a Simple Process Drives Safety Compliance
Safety management systems have come a long way in the last 250 years. Just think back to workplace conditions during the Industrial Revolution – almost no pay, child labour, very long hours, and extremely dangerous work conditions with exposure to chemicals, accident-prone machinery, and no WHS requirements whatsoever.
But this has changed over the years. Legal reforms and acts were introduced – the Factory Act, the Employer’s Liability Act, and finally, the 1974 Health and Safety at Work Act. This legal document became the foundation for workplace health and safety processes in the UK and the rest of the world. And it led to the increasingly more complex safety processes we have today.
The core purpose of WHS is to keep people safe. Simple. With the increasing complexity of requirements and standards, Business owners, project managers and safety officers alike have to be careful of falling into the trap of using compliance to document requirements like the SWMS as their main measure of WHS compliance. This article looks at why adhering to document requirements is a poor standalone indicator of compliance. We also suggest how a simple safety process drives the success of your WHS compliance.
Documents are Symbols of a Process
Safety isn’t symbolic. It is real and should be treated in the real world, not on a document. Safety management systems do involve documents, but they symbolise a process. For example, a SWMS is a safety planning tool that identifies the risks of high risk construction work and the actions taken to manage those risks. It symbolises the process you are going to take when dealing with the risks and making sure your workplace and its workers are safe from those risks. When it’s under the (judges) hammer, the process symbolised (documented) matters most – not the symbol or the document itself.
Downloading a generic template for your SWMS, JSA, or any other safety document is like taking the symbol without taking the process it represents. And that defeats the whole point of your safety management system and its documents. To comply with WHS requirements, you should be focusing on the processes required to keep your workplace and its workers safe – not just on the documents themselves.
WHS audits look at whether you have followed an effective process that actively reduces the risks in your workplace. They care about if you have actually provided a safe work environment. Not simply whether you have ticked the box of completing a piece of paperwork.
In 2013, The Supreme Court Qld in a case against a QLD construction company for the death of two workers cited:
“work practices focused too much on the work performed onsite and did not pay adequate attention to the dangers presented by the conditions of the site itself”
In other words, not considering risks on the ground, in the real world can have significant impacts when taken to the extremes. Focussing too hard on the details of the tasks to be completed can lead to ignoring all the risks that are actively present
What you focus on matters. And if you want to pass your WHS audit and actually keep your workers safe, then it’s time to focus on the safety management process behind the symbols and documents.
But I still go through a process when filling in a template?
Safety management systems aren’t just about the symbols. They’re about the processes behind them. But you may be wondering – isn’t downloading a generic template still technically a process? Sure. But think about this. What process is more effective at satisfying the Work Health and Safety Act requirement to provide a safe work environment? Is it:
- Find a generic SWMS template on Google, Officeworks or other source
- Complete the boxes provided by the template as best as you can
- Gather up or seek out workers individually and gather signatures
- Store it onsite until the work is done
- Transferring the document to a folder in your office when you are done with the site
Or:
- Identify a the risks onsite, in person
- Build a new SWMS or modify the existing version to cover all task & site-specific risks that are present. Pushed to everyone to sign.
- Monitor how measures are being implemented while work is being completed with real time automated risk rating notifications
- Review by anyone relevant once the work has been completed
- Automatic document storage once complete for any future audits, follow-ups, or learning
From a legal standpoint, the second option is better,
The very purpose of developing a SWMS is to ensure that employers and workers have taken the time to identify the high-risk tasks to be done on site. And then, it is to develop measures to manage these risks and tasks in the context of the work being done. The very nature of a SWMS is that it is specific. It is created specifically in response to a specific site, specific tasks, and specific risks. A generic templated SWMS will not meet the intention behind WHS requirements. Instead, it will defeat the real power of the SWMS and even take away from your safety management.
As WorkSafe Victoria explains, “our concern is not what is written but what actually happens”. A generic SWMS is a symbol of safety that only provides guidance. To focus on the process and comply with WHS requirements, your SWMS and other safety documents need to be customised. It is the second process that is more likely to pass a WHS audit because it demonstrates an active approach to creating a safe work environment. And it is the first process that will get a much more severe punishment when a safety incident does happen, even though both processes are represented by the same type of document.
How to Prioritize the Process
The simplest way to boost the effectiveness of your safety process is to use a digital safety platform like SafeWorkPro. While you can do your safety management physically or digitally, doing it digitally is what will make the difference. Why?
Safety management software simplifies your safety management. Turning a complex process into a simple, easy to understand workflow that allows for an easier way to assess, mitigate, monitor and review workplace risks of all nature. It makes sure that your safety management system is customised, comprehensive, and lets you focus on the process. Leave the document creation, distribution and storage to the software. With safety management software, you can seamlessly customise, prioritise, and ensure your safety management system and its processes exceed WHS regulations.
SafeWorkPro is the Australian safety management software that can make sure your workplace prioritises the process over the symbols.
- Customise your SWMS, JSA, or other safety documents specifically to your worksite using our flexible document builder
- Make sure your specific workplace risks are managed and your workers are safe
- Ensure your company truly complies with WHS requirements
Do all of this seamlessly and in one place with the SafeWorkPro platform. Click the button below to find out more.
More From The SafeWorkPro Blog
Hazard Assessment in Confined Spaces
In the previous article ‘Working in Confined Spaces Risk Assessment’, we looked at the definition of ‘confined space’ and what generic risks and hazards are associated with it. It is clear that confined spaces fall under the mandate of what constitutes high risk construction work. Based on the Work Health and Safety Regulation 2011, Safe Work Australia outlines many of the considerable hazards involving with working in confined spaces but there substantial details to each of these that should be noted.
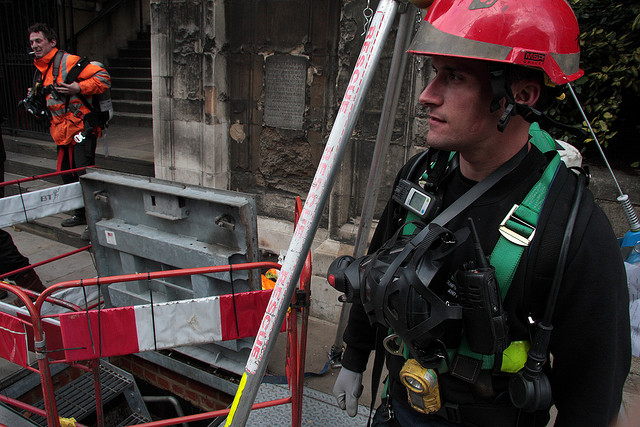
o Presence of harmful airborne contaminants
o Unsafe oxygen level caused when oxygen in the atmosphere is:
- displaced by gases produced during biological processes, for example, methane in a sewer
- displaced during purging of a confined space with an inert gas to remove flammable or toxic fumes
- depleted inside metal tanks and vessels through surface oxidation (for example, when rust forms)
- consumed during combustion of flammable substances
- absorbed or reacts with grains, wood chips, soil or chemicals in sealed silos.
- reacts with chemicals that increase risk of explosion or fire (eg hydrogen peroxide)
- leaks from oxygen tank or fitting during use of oxy-acetylene equipment
o Fire and explosion
- Flammable gas, mist or vapour in atmosphere exceeds 5% of its lower explosive limit (LEL)
- Evaporation of flammable residue
- Use of flammable materials
- Chemical reaction (eg build up methane from sewer)
- Presence of combustible dust (flour in silo)
o Introduction of an ignition source into atmosphere. Such sources may include:
- open flames and hot surfaces
- electrical equipment
- internal combustion engines
- metal tools striking metal surfaces
- spark-producing equipment for example grinding wheels
- static electricity
o Engulfment leading to asphyxiation
- Confined spaces with stored materials including plastics, sand, liquids, fertiliser, grain, coal, coal products, fly ash, animal feed and sewage
o Uncontrolled introduction of substances
- Substances include steam, water or other liquids, gases or solids that may result in a person drowning, being overcome by fumes or other harm
- Build up of exhaust fumes, including carbon monoxide, from nearby vehicles including LPG forklifts
o Contact with biological agents
- Such as micro-organism like virus, bacteria or fungi which can cause infectious diseases, dermatitis or lung conditions such as hypersensitivity pneumonitis
- Sewers, grain silos and manure pits are confined spaces where biological hazards may be present
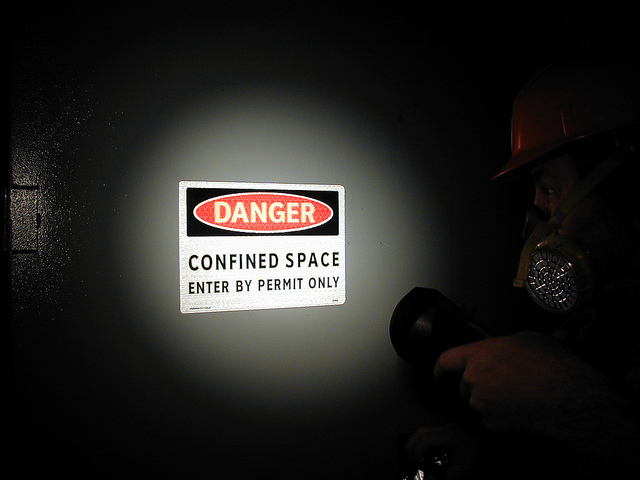
o Exposure to mechanical hazards
- The entanglement, crushing, cutting, piercing or shearing of parts of a person’s body from mechanical hazards including augers, agitators, blenders, mixers and stirrers
o Contact with electrical hazards
- Electrocution, shocks or burns caused by cables, transformers, capacitors, relays, exposed terminals and wet surfaces where electrical circuit and electrically powered plant are used
o Skin contact with hazardous substances
- Increased likelihood of skin contact with contaminated surfaces resulting in burns, irritation, allergic dermatitis or long-term systematic effects
o Noise
- Noise caused by plant, work method or process may be amplified due to noise reflections off hard surfaces
o Manual tasks
- Physical restraints of confined space may exacerbate hazards relating to manual tasks
- Further hazards may arise from use of PPE that restricts movement, grip and mobility
o Radiation
- Sources of radiation may include x-rays, lasers, welding flash, radio frequency and microwaves
o Environmental hazards
- Factors that contribute or cause harm such as heat or cold stress, inadequate lighting
- Slips, trips and falls
o Control methods for hazards near or adjacent to a confined space (pg 19)
- Hazards outside the confined space: ie vertical opening = risk of falling in space
- Traffic hazards should the confined space be located under or near a road
- Exhaust gas from a adjacent vehicle or machine may contaminate the confined area
- Confined areas adjacent to work involving flammable substances
Risk assessment for chemicals checklist
When working with hazardous substances or chemicals, it is especially important to effectively complete risk assessments. One way to help in this area is to complete a risk assessment checklist before beginning any high risk construction work.
A hazardous substances risk assessment is a useful component of safe operating procedures but risk assessment checklists are a great way to double check any workplace precautions. This is beneficial due to the increased risks in construction presented by the potential long-term health effects of exposure to hazardous substances.
The below is a risk management checklist based on the codes of practices for managing risks of hazardous chemicals.
1: Does a risk assessment need to be carried out?
2: Has it been decided who will carry out the risk assessment?
3a: Have all the hazardous chemicals in the workplace been identified?
3b: Has a hazardous chemical register been produced?
· A register is a list of hazardous substances, accompanied by a safety data sheet, and easily accessed by all duty holders
4: Has information about the hazardous chemical been identified?
5a: Have other previous relevant records, including risk assessments, been checked?
· If yes: have any specific hazardous substances been assessed as high risk?
6: Does the hazardous substance have any health hazards?
7: Does the hazardous substance have any physicochemical hazards?
8: Does the hazardous substance have an exposure stands?
· Refer to Workplace Exposure Standards for Airborne Contaminants
9: Do workers involved in the work related to hazardous substances require health monitoring?
· Refer to Part 7.1, Div. 6 and Schedule 14 of the WHS Regulation 2011
10: Is there a potential for workers to be exposed to hazardous substances at the workplace including by-products and waste?
· Consider these questions:
o Is the substance released into the work area’s atmosphere?
o Are people located in the immediate vicinity?
o How long are workers exposed for?
o Are there risks involved in the storage and/or transportation of the hazardous substance?
11: Are the controls measures specified in the risk assessment effective in controlling hazards and reviewed regularly?
12: Are risks not significant, significant but adequately controlled, significant but not adequately controlled or uncertain?
13: Have any actionable safety procedures been conducted as a result of question 12?
14: Has the risk assessment been recorded for future reference?