How a Simple Process Drives Safety Compliance
Safety management systems have come a long way in the last 250 years. Just think back to workplace conditions during the Industrial Revolution – almost no pay, child labour, very long hours, and extremely dangerous work conditions with exposure to chemicals, accident-prone machinery, and no WHS requirements whatsoever.
But this has changed over the years. Legal reforms and acts were introduced – the Factory Act, the Employer’s Liability Act, and finally, the 1974 Health and Safety at Work Act. This legal document became the foundation for workplace health and safety processes in the UK and the rest of the world. And it led to the increasingly more complex safety processes we have today.
The core purpose of WHS is to keep people safe. Simple. With the increasing complexity of requirements and standards, Business owners, project managers and safety officers alike have to be careful of falling into the trap of using compliance to document requirements like the SWMS as their main measure of WHS compliance. This article looks at why adhering to document requirements is a poor standalone indicator of compliance. We also suggest how a simple safety process drives the success of your WHS compliance.
Documents are Symbols of a Process
Safety isn’t symbolic. It is real and should be treated in the real world, not on a document. Safety management systems do involve documents, but they symbolise a process. For example, a SWMS is a safety planning tool that identifies the risks of high risk construction work and the actions taken to manage those risks. It symbolises the process you are going to take when dealing with the risks and making sure your workplace and its workers are safe from those risks. When it’s under the (judges) hammer, the process symbolised (documented) matters most – not the symbol or the document itself.
Downloading a generic template for your SWMS, JSA, or any other safety document is like taking the symbol without taking the process it represents. And that defeats the whole point of your safety management system and its documents. To comply with WHS requirements, you should be focusing on the processes required to keep your workplace and its workers safe – not just on the documents themselves.
WHS audits look at whether you have followed an effective process that actively reduces the risks in your workplace. They care about if you have actually provided a safe work environment. Not simply whether you have ticked the box of completing a piece of paperwork.
In 2013, The Supreme Court Qld in a case against a QLD construction company for the death of two workers cited:
“work practices focused too much on the work performed onsite and did not pay adequate attention to the dangers presented by the conditions of the site itself”
In other words, not considering risks on the ground, in the real world can have significant impacts when taken to the extremes. Focussing too hard on the details of the tasks to be completed can lead to ignoring all the risks that are actively present
What you focus on matters. And if you want to pass your WHS audit and actually keep your workers safe, then it’s time to focus on the safety management process behind the symbols and documents.
But I still go through a process when filling in a template?
Safety management systems aren’t just about the symbols. They’re about the processes behind them. But you may be wondering – isn’t downloading a generic template still technically a process? Sure. But think about this. What process is more effective at satisfying the Work Health and Safety Act requirement to provide a safe work environment? Is it:
- Find a generic SWMS template on Google, Officeworks or other source
- Complete the boxes provided by the template as best as you can
- Gather up or seek out workers individually and gather signatures
- Store it onsite until the work is done
- Transferring the document to a folder in your office when you are done with the site
Or:
- Identify a the risks onsite, in person
- Build a new SWMS or modify the existing version to cover all task & site-specific risks that are present. Pushed to everyone to sign.
- Monitor how measures are being implemented while work is being completed with real time automated risk rating notifications
- Review by anyone relevant once the work has been completed
- Automatic document storage once complete for any future audits, follow-ups, or learning
From a legal standpoint, the second option is better,
The very purpose of developing a SWMS is to ensure that employers and workers have taken the time to identify the high-risk tasks to be done on site. And then, it is to develop measures to manage these risks and tasks in the context of the work being done. The very nature of a SWMS is that it is specific. It is created specifically in response to a specific site, specific tasks, and specific risks. A generic templated SWMS will not meet the intention behind WHS requirements. Instead, it will defeat the real power of the SWMS and even take away from your safety management.
As WorkSafe Victoria explains, “our concern is not what is written but what actually happens”. A generic SWMS is a symbol of safety that only provides guidance. To focus on the process and comply with WHS requirements, your SWMS and other safety documents need to be customised. It is the second process that is more likely to pass a WHS audit because it demonstrates an active approach to creating a safe work environment. And it is the first process that will get a much more severe punishment when a safety incident does happen, even though both processes are represented by the same type of document.
How to Prioritize the Process
The simplest way to boost the effectiveness of your safety process is to use a digital safety platform like SafeWorkPro. While you can do your safety management physically or digitally, doing it digitally is what will make the difference. Why?
Safety management software simplifies your safety management. Turning a complex process into a simple, easy to understand workflow that allows for an easier way to assess, mitigate, monitor and review workplace risks of all nature. It makes sure that your safety management system is customised, comprehensive, and lets you focus on the process. Leave the document creation, distribution and storage to the software. With safety management software, you can seamlessly customise, prioritise, and ensure your safety management system and its processes exceed WHS regulations.
SafeWorkPro is the Australian safety management software that can make sure your workplace prioritises the process over the symbols.
- Customise your SWMS, JSA, or other safety documents specifically to your worksite using our flexible document builder
- Make sure your specific workplace risks are managed and your workers are safe
- Ensure your company truly complies with WHS requirements
Do all of this seamlessly and in one place with the SafeWorkPro platform. Click the button below to find out more.
More From The SafeWorkPro Blog
Job Safety Analysis Forms
Everyone hates paperwork but even in this digital age of instant messaging and computer technology, it remains a necessary evil. Job safety analysis forms are an essential part of the risk assessment process and crucial to job safety.
Although OHS legislation Australia is complicated and the job safety analysis process is lengthy, the paperwork itself is easy enough to understand. Just have a look at this job safety analysis example taken from the Victorian WorkCover Authority.
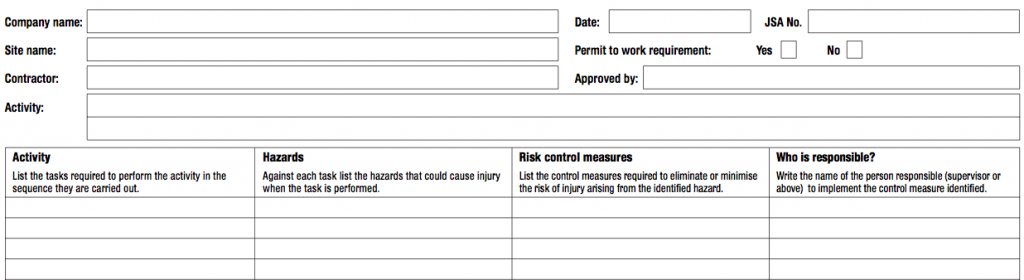
This job safety analysis sheet is simple enough. The high risk work, associated hazards and the control measures are listed next to each other while there’s space for the responsible duty holder to sign off. At the top of the job safety analysis form are the company and workplace details, date, activity description and space for the person conducting a business or undertaking (PCBU) to approve the job risk assessment.
So job safety analysis forms are pretty easy to understand but they are still one of those annoying tasks that just have to be done regardless of how stressed the paperwork makes you feel.
But there is a better way.
Job safety analysis software takes the paperwork out of the risk assessment process and gives you more time to get on with other work. This software solution is even easier to understand than the job safety analysis forms. Click here to learn more.
Workplace Safety Checklist
Across all industries and workplaces here are common factors that should be included in a safety checklist. These are vital safeguards that work not only to normalise a culture of safety but also to prevent workplace accidents. But what exactly does a safety checklist look like? Well for starters it is more than just a […]
The SafeWorkPro Safety Management Dashboard
No matter the type of industry, whether it’s mining, construction, manufacturing or even basic labour, risk is a constantly evolving threat. Dangers associated with any type of work threaten not only the well-being of workers, but also how productive and profitable a business can be.
The logic is simple. An effective and efficient OHS management system will result in quicker, safer and more compliant safety procedures. This means workers spend less time writing safety documents and more time getting the job done. Moreover, an efficient management system gives safety managers the tools to improve safe work practices and boost productivity.
Therefore safe systems of work need to be established which are smart and flexible enough to adapt with continually changing workplace environments. Previously on the SafeWorkPro Blog, we’ve written about how our software empowers managers and workers to create their own safety documents but now there is another feature which produces even better OHS results.
The Dashboard: using data driven decision-making to improve OHS procedures
A decision that is backed up by strong data will always produce better results. That’s why the dashboard feature has been implemented into the SafeWorkPro software. The dashboard is a place for managers to track the progress of their OHS policies and procedures, and see how well these are actually being implemented. Data relating to what safety document was used for a job, who completed it and the risk involved, are just some of the business insights that the dashboard feature provides. In all, four components break the data down into easy to understand terms.
1: The number of safety documents for each site
Understanding what safety documents are being used for which job site is important for helping managers keep their finger on the pulse of a business. The image to the right is taken from the Dashboard of an existing SafeWorkPro user and shows which jobs have the most risk assessments associated with it. This information can tell a manager where most of their workforce is being used and which jobs require the most occupational health and safety procedures.

2: The cumulative safety document count
This line graph shows the number of risk assessments a business has produced over a long period of time. The data is broken into monthly figures, which provides managers with an insight into the number of completed safety documents as well as any rise or drop that strays from the overall trend.
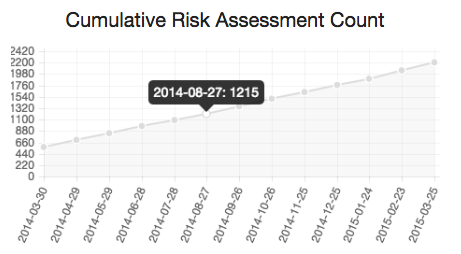
3: Today’s safety documents
Knowing who is doing a job is just as important as knowing what the job is. This part of the Dashboard shows which worker completed the safety document (in this case a risk assessment) for which job. The steps associated with the safety document are listed as well as the number of hazards. This instantly shows which job is the most risky and allows managers to review the completed safety document, thus improving the efficiency of how documents are shared and complied with.
This feature also allows managers to search for specific dates and find the safety documents associated with any job no matter how long ago it was finished. Moreover, a PDF of the document can be downloaded which makes satisfying compliance requests as easy as sending an email.
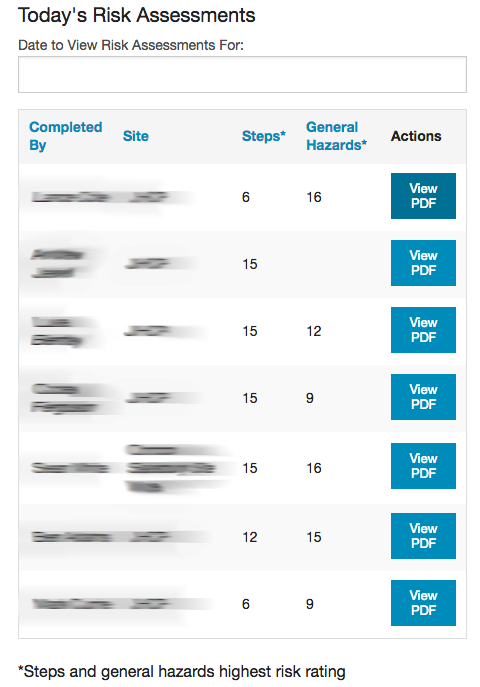
4: The safety document count
This line graph examines the number of safety documents completed on each day of any given week. It provides a short term insight into daily safe work practices conducted by workers as well as the OHS demands of each job on the respective day that it’s being worked on. For instance, on the left graph the number of completed safety
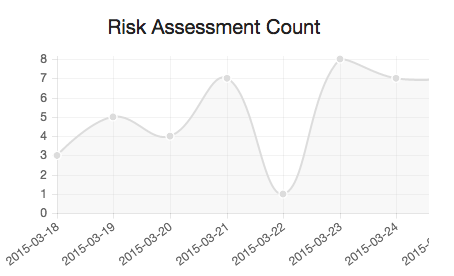
Summary
Although occupational health and safety is often viewed as a drain on time, it does not necessarily have to be. The Dashboard is the perfect place for managers looking optimise or streamline parts of their business. It benefits management by offering in-depth data that can be used as a basis for future decision making while it provides workers with an easy to use platform that tracks their current and past safety documents. In all, the Dashboard is another great feature for users of the SafeWorkPro software. If you would like to boost productivity without compromising workplace safety, try SafeWorkPro for free.