How a Simple Process Drives Safety Compliance
Safety management systems have come a long way in the last 250 years. Just think back to workplace conditions during the Industrial Revolution – almost no pay, child labour, very long hours, and extremely dangerous work conditions with exposure to chemicals, accident-prone machinery, and no WHS requirements whatsoever.
But this has changed over the years. Legal reforms and acts were introduced – the Factory Act, the Employer’s Liability Act, and finally, the 1974 Health and Safety at Work Act. This legal document became the foundation for workplace health and safety processes in the UK and the rest of the world. And it led to the increasingly more complex safety processes we have today.
The core purpose of WHS is to keep people safe. Simple. With the increasing complexity of requirements and standards, Business owners, project managers and safety officers alike have to be careful of falling into the trap of using compliance to document requirements like the SWMS as their main measure of WHS compliance. This article looks at why adhering to document requirements is a poor standalone indicator of compliance. We also suggest how a simple safety process drives the success of your WHS compliance.
Documents are Symbols of a Process
Safety isn’t symbolic. It is real and should be treated in the real world, not on a document. Safety management systems do involve documents, but they symbolise a process. For example, a SWMS is a safety planning tool that identifies the risks of high risk construction work and the actions taken to manage those risks. It symbolises the process you are going to take when dealing with the risks and making sure your workplace and its workers are safe from those risks. When it’s under the (judges) hammer, the process symbolised (documented) matters most – not the symbol or the document itself.
Downloading a generic template for your SWMS, JSA, or any other safety document is like taking the symbol without taking the process it represents. And that defeats the whole point of your safety management system and its documents. To comply with WHS requirements, you should be focusing on the processes required to keep your workplace and its workers safe – not just on the documents themselves.
WHS audits look at whether you have followed an effective process that actively reduces the risks in your workplace. They care about if you have actually provided a safe work environment. Not simply whether you have ticked the box of completing a piece of paperwork.
In 2013, The Supreme Court Qld in a case against a QLD construction company for the death of two workers cited:
“work practices focused too much on the work performed onsite and did not pay adequate attention to the dangers presented by the conditions of the site itself”
In other words, not considering risks on the ground, in the real world can have significant impacts when taken to the extremes. Focussing too hard on the details of the tasks to be completed can lead to ignoring all the risks that are actively present
What you focus on matters. And if you want to pass your WHS audit and actually keep your workers safe, then it’s time to focus on the safety management process behind the symbols and documents.
But I still go through a process when filling in a template?
Safety management systems aren’t just about the symbols. They’re about the processes behind them. But you may be wondering – isn’t downloading a generic template still technically a process? Sure. But think about this. What process is more effective at satisfying the Work Health and Safety Act requirement to provide a safe work environment? Is it:
- Find a generic SWMS template on Google, Officeworks or other source
- Complete the boxes provided by the template as best as you can
- Gather up or seek out workers individually and gather signatures
- Store it onsite until the work is done
- Transferring the document to a folder in your office when you are done with the site
Or:
- Identify a the risks onsite, in person
- Build a new SWMS or modify the existing version to cover all task & site-specific risks that are present. Pushed to everyone to sign.
- Monitor how measures are being implemented while work is being completed with real time automated risk rating notifications
- Review by anyone relevant once the work has been completed
- Automatic document storage once complete for any future audits, follow-ups, or learning
From a legal standpoint, the second option is better,
The very purpose of developing a SWMS is to ensure that employers and workers have taken the time to identify the high-risk tasks to be done on site. And then, it is to develop measures to manage these risks and tasks in the context of the work being done. The very nature of a SWMS is that it is specific. It is created specifically in response to a specific site, specific tasks, and specific risks. A generic templated SWMS will not meet the intention behind WHS requirements. Instead, it will defeat the real power of the SWMS and even take away from your safety management.
As WorkSafe Victoria explains, “our concern is not what is written but what actually happens”. A generic SWMS is a symbol of safety that only provides guidance. To focus on the process and comply with WHS requirements, your SWMS and other safety documents need to be customised. It is the second process that is more likely to pass a WHS audit because it demonstrates an active approach to creating a safe work environment. And it is the first process that will get a much more severe punishment when a safety incident does happen, even though both processes are represented by the same type of document.
How to Prioritize the Process
The simplest way to boost the effectiveness of your safety process is to use a digital safety platform like SafeWorkPro. While you can do your safety management physically or digitally, doing it digitally is what will make the difference. Why?
Safety management software simplifies your safety management. Turning a complex process into a simple, easy to understand workflow that allows for an easier way to assess, mitigate, monitor and review workplace risks of all nature. It makes sure that your safety management system is customised, comprehensive, and lets you focus on the process. Leave the document creation, distribution and storage to the software. With safety management software, you can seamlessly customise, prioritise, and ensure your safety management system and its processes exceed WHS regulations.
SafeWorkPro is the Australian safety management software that can make sure your workplace prioritises the process over the symbols.
- Customise your SWMS, JSA, or other safety documents specifically to your worksite using our flexible document builder
- Make sure your specific workplace risks are managed and your workers are safe
- Ensure your company truly complies with WHS requirements
Do all of this seamlessly and in one place with the SafeWorkPro platform. Click the button below to find out more.
More From The SafeWorkPro Blog
Risk Management Framework
The management of risk is defined by a framework of control measures which prioritise the highest forms of protection down to the lowest. This risk management framework, or hierarchy as it is also known, breaks various risk control methods into three levels ranging from most effective to the least reliable. Under OHS laws and regulations, duty holders are required to work through this framework when conducing risk management in construction.
This is a fundamental part of knowing how to perform a risk assessment.
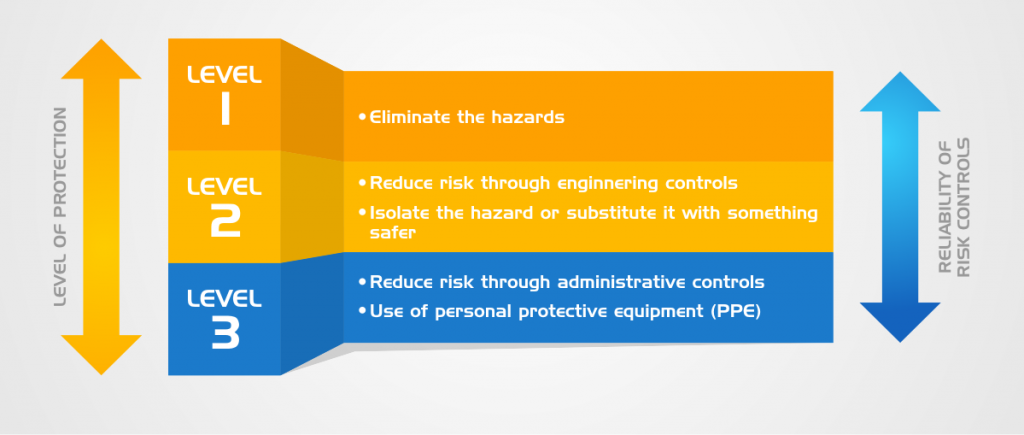
Level 1 of risk management strategies
The best way to reduce risk in a workplace is by eliminating all hazards completely. For instance, if there is a risk of falling from heights then the best risk management strategy would be to work from the ground level instead. The same applies for hazards like dangerous chemicals or trips and slips.
The rule of ‘reasonable practicality’ states that if eliminating the hazard makes it impossible for the construction service to be delivered then the risks associated with the hazard should be eliminated. An example of this would be wearing a safety harnesses and having a supervisor while working at heights (see level 2).
Level 2 of risk management strategies
If eliminating a hazard or all of the risks associated with it is not reasonably practicable then there are several other approaches that can minimise the involved risks. These risk management tools and techniques include:
- The use of risk assessment engineering controls (eg warning signage, noise barriers, maintenance of machinery)
- Substituting the hazard with a safer alternative
- Isolating the hazard from workers and other affected persons
Level 3 of risk management strategies
This is the least effective and least reliable risk management system because it relies on human behaviour and supervision. When used in isolation, level three of the risk management framework should be carried out in line with appropriate administrative controls (eg rest breaks, job rotations) and with the use of personal protective equipment (PPE).
In regards to the proper use of PPE, regulation 44-47 of the Work Health and Safety Codes of Practice state that the equipment must be:
- “selected to minimise the risk to health and safety”
- “suitable for the nature of the work and any hazard associated with the work”
- “maintained, repaired or replaced so it continues to minimise the risk”
- “a suitable size and fit and [be] reasonably comfortable for the person wearing it”
- “used and worn by the worker, so far is reasonably practicable”
- worn “…in accordance with any information, training or reasonable instruction.”
It is recommended that level 3 risk management strategies be used in conjunction with methods from level 2 or 1 where possible.
For more information on occupational health and safety regulations or on the risk assessment process, check out the SafeWorkPro Blog.
Risk Assessment Tools
The risk assessment workflow traditionally associated with high risk construction work has a major flaw that many in the industry don’t know exists. Paper-based risk assessments, although standard industry practice, have a significant time-cost that cuts into business productivity and complicates safe work practices. Yet there are risk assessment tools available that can remove this issue without undermining workplace health and safety.
These tools are widely known as safety compliance software but are called other names including risk management tools and construction risk assessment software. All these tools relate to the risk assessment process – ie how construction workers identify hazards and implement control measures.
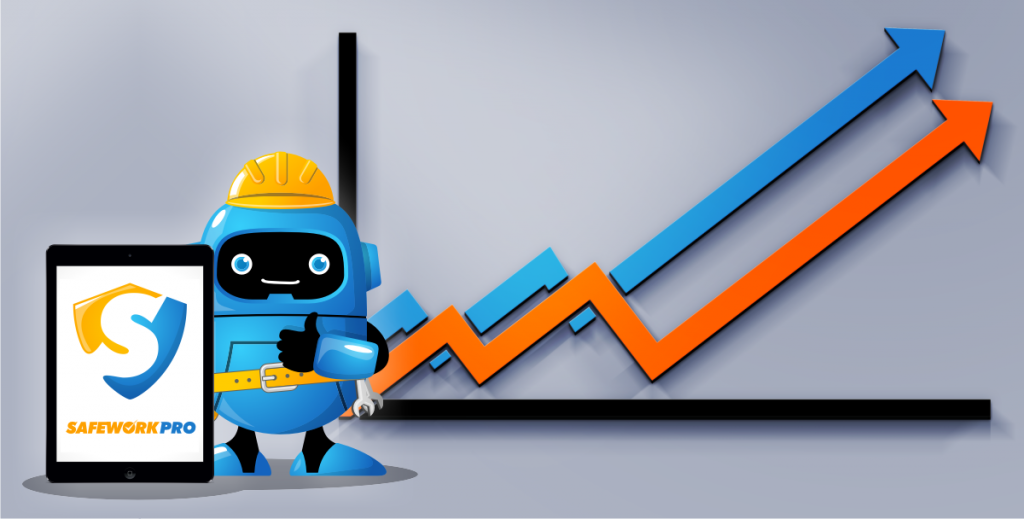
Although vital to safe work practices, risk assessment paperwork is a burden on employee workloads and backend administration. It takes up time on the worksite and back at the office when the paperwork is completed and filed. Yet as software alternatives continue to develop, new risk analysis tools are entering the market and they have the ability to streamline this entire process.
These digital tools take the paperwork out of the risk assessment process. Automated forms take the user through the risk assessment process step by step – just like in a traditional risk analysis table – but every entry is saved and can be used in a future worksite of a similar nature. At every point in the various stages of risk assessment, risk assessment tools like software aim to increase time efficiency and in turn business productivity.
There are many software alternatives to the paper-based risk assessment process in the market but SafeWorkPro was developed in direct consultation with electrical contractors and workers. For more information on the SafeWorkPro software, you can read What is SafeWorkPro? or you can checkout our blog.
Learn How To Create a Safety Culture with Software
Imagine being able to devise, use and share even the most complicated safety documents on your smart phone?
Well you can stop imagining. This will soon become a reality.
Recent innovations in occupational health and safety software mean that safety paperwork like health and safety performance indicators and a material data sheet for chemicals can now be created by individual businesses. The range of safety documents applicable to this new system is almost unlimited which means workers of any type will be empowered to address their workplace’s safety culture and risk.
Software like SafeWorkPro provides workers and managers alike with the tools to create their own safety documents, regardless of their type of work involves. This tool removes the hassle of paperwork from OHS policy and procedures while promoting a safer work environment.
The benefits for workers are quite clear.
Provides a flexible OHS management system
- SafeWorkPro provides workers with the ability to create safety documents that can be designed to best suit an individual worksite. This means safer work practices and an improved level of compliance. It also means that workers won’t be wasting time with documents not suited for their specific working environment.
Cultivates a strong safety culture
- By having workers directly involved in the creation of safety documents, SafeWorkPro reinforces the importance of proper health and safety practices into their daily working habits. This in turns brings safety to the front of each worker’s mind, maintains an active knowledge of safe work practices and fosters an improved workplace safety culture.
The involvement of workers in the creation of safety documents is key to the success of SafeWorkPro. As outlined in the Australian Work Health and Safety Strategy 2012-2022, “Within organisations, leaders promote positive cultures by demonstrating a commitment to…role clarity, worker involvement and workgroup cohesion.”
This is the cornerstone of SafeWorkPro – empowering workers with more efficient and flexible safety software systems.