How a Simple Process Drives Safety Compliance
Safety management systems have come a long way in the last 250 years. Just think back to workplace conditions during the Industrial Revolution – almost no pay, child labour, very long hours, and extremely dangerous work conditions with exposure to chemicals, accident-prone machinery, and no WHS requirements whatsoever.
But this has changed over the years. Legal reforms and acts were introduced – the Factory Act, the Employer’s Liability Act, and finally, the 1974 Health and Safety at Work Act. This legal document became the foundation for workplace health and safety processes in the UK and the rest of the world. And it led to the increasingly more complex safety processes we have today.
The core purpose of WHS is to keep people safe. Simple. With the increasing complexity of requirements and standards, Business owners, project managers and safety officers alike have to be careful of falling into the trap of using compliance to document requirements like the SWMS as their main measure of WHS compliance. This article looks at why adhering to document requirements is a poor standalone indicator of compliance. We also suggest how a simple safety process drives the success of your WHS compliance.
Documents are Symbols of a Process
Safety isn’t symbolic. It is real and should be treated in the real world, not on a document. Safety management systems do involve documents, but they symbolise a process. For example, a SWMS is a safety planning tool that identifies the risks of high risk construction work and the actions taken to manage those risks. It symbolises the process you are going to take when dealing with the risks and making sure your workplace and its workers are safe from those risks. When it’s under the (judges) hammer, the process symbolised (documented) matters most – not the symbol or the document itself.
Downloading a generic template for your SWMS, JSA, or any other safety document is like taking the symbol without taking the process it represents. And that defeats the whole point of your safety management system and its documents. To comply with WHS requirements, you should be focusing on the processes required to keep your workplace and its workers safe – not just on the documents themselves.
WHS audits look at whether you have followed an effective process that actively reduces the risks in your workplace. They care about if you have actually provided a safe work environment. Not simply whether you have ticked the box of completing a piece of paperwork.
In 2013, The Supreme Court Qld in a case against a QLD construction company for the death of two workers cited:
“work practices focused too much on the work performed onsite and did not pay adequate attention to the dangers presented by the conditions of the site itself”
In other words, not considering risks on the ground, in the real world can have significant impacts when taken to the extremes. Focussing too hard on the details of the tasks to be completed can lead to ignoring all the risks that are actively present
What you focus on matters. And if you want to pass your WHS audit and actually keep your workers safe, then it’s time to focus on the safety management process behind the symbols and documents.
But I still go through a process when filling in a template?
Safety management systems aren’t just about the symbols. They’re about the processes behind them. But you may be wondering – isn’t downloading a generic template still technically a process? Sure. But think about this. What process is more effective at satisfying the Work Health and Safety Act requirement to provide a safe work environment? Is it:
- Find a generic SWMS template on Google, Officeworks or other source
- Complete the boxes provided by the template as best as you can
- Gather up or seek out workers individually and gather signatures
- Store it onsite until the work is done
- Transferring the document to a folder in your office when you are done with the site
Or:
- Identify a the risks onsite, in person
- Build a new SWMS or modify the existing version to cover all task & site-specific risks that are present. Pushed to everyone to sign.
- Monitor how measures are being implemented while work is being completed with real time automated risk rating notifications
- Review by anyone relevant once the work has been completed
- Automatic document storage once complete for any future audits, follow-ups, or learning
From a legal standpoint, the second option is better,
The very purpose of developing a SWMS is to ensure that employers and workers have taken the time to identify the high-risk tasks to be done on site. And then, it is to develop measures to manage these risks and tasks in the context of the work being done. The very nature of a SWMS is that it is specific. It is created specifically in response to a specific site, specific tasks, and specific risks. A generic templated SWMS will not meet the intention behind WHS requirements. Instead, it will defeat the real power of the SWMS and even take away from your safety management.
As WorkSafe Victoria explains, “our concern is not what is written but what actually happens”. A generic SWMS is a symbol of safety that only provides guidance. To focus on the process and comply with WHS requirements, your SWMS and other safety documents need to be customised. It is the second process that is more likely to pass a WHS audit because it demonstrates an active approach to creating a safe work environment. And it is the first process that will get a much more severe punishment when a safety incident does happen, even though both processes are represented by the same type of document.
How to Prioritize the Process
The simplest way to boost the effectiveness of your safety process is to use a digital safety platform like SafeWorkPro. While you can do your safety management physically or digitally, doing it digitally is what will make the difference. Why?
Safety management software simplifies your safety management. Turning a complex process into a simple, easy to understand workflow that allows for an easier way to assess, mitigate, monitor and review workplace risks of all nature. It makes sure that your safety management system is customised, comprehensive, and lets you focus on the process. Leave the document creation, distribution and storage to the software. With safety management software, you can seamlessly customise, prioritise, and ensure your safety management system and its processes exceed WHS regulations.
SafeWorkPro is the Australian safety management software that can make sure your workplace prioritises the process over the symbols.
- Customise your SWMS, JSA, or other safety documents specifically to your worksite using our flexible document builder
- Make sure your specific workplace risks are managed and your workers are safe
- Ensure your company truly complies with WHS requirements
Do all of this seamlessly and in one place with the SafeWorkPro platform. Click the button below to find out more.
More From The SafeWorkPro Blog
Meet the Regulators: Workplace Health and Safety Queensland
Workplace Health and Safety Queensland (WHSQ) is the peak authority for OHS regulations in Queensland. Although other statutory bodies play a role in Queensland health and safety, WHSQ is the main regulator and is responsible for the enforcement of OHS laws and compliance. To work in Queensland within the current framework of occupational health and safety legislation as outlined by Safe Work Australia, you need to understand who WHSQ is, what its role entails, and the extent of its legal reach.
Let’s start off with ‘the who’ and WHSQ is part of the Department of Justice and Attorney-General. WHSQ is governed by the work health and safety board, which is comprised of 11 members from employer, employee and industry groups. The board, in conjunction with the industry sector standing committee, provide Workplace Health and Safety Queensland with advice for issues in:
• Construction
• Manufacturing
• Rural
• Community
• Health services
• Retail
• Wholesale
• Hospitality
• Recreation
• Transport
• Storage
Queensland safety legislation is based on the model framework from Safe Work Australia but its role goes beyond basic workplace regulations. On top of licensing and registrations for high risk work and OHS training, WHSQ also reviews the Work Health and Safety Act, makes policy recommendations to the Attorney-General and conducts routine workplace inspections. The regulatory role of WHSQ includes a wide range compliance and enforcement options. These include:
• Issuing advice, information and infringement notices
• On the spot fines
• Seizure of equipment or substances
• Suspension of license or accreditation
• Enforceable undertakings (legally binding agreements)
• Prosecutions
• Workplace interventions and audits
Understanding the scale of WHSQ’s powers will ensure you don’t receive any penalties or worse. But ultimately the only way to ensure the health and safety of your workers while remaining compliant with OHS policy is by implementing a modern, software based risk assessment process.
What Are Your Online Risk Assessment Options?
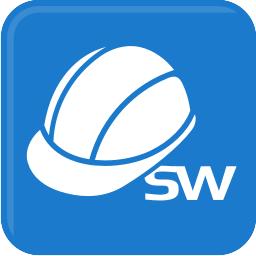
The evolution of risk management in software engineering has produced risk assessment software that ranges from the obsolete to the irrelevant. As Australia’s vast array of OHS laws and regulations change, it’s difficult to pinpoint what software risk assessment should be used for.
Some early editions involved writing a risk assessment online but were rendered useless if a construction worker happened to be on a site without internet access.
More recent forms of internet safety software hold many advantages for risk and compliance but are so complicated that the average worker – or IT technician for that matter – is unable to understand it.
So the search for useful online risk assessments has resulted in products that range from the obsolete to the irrelevant. But construction safety software is starting to gain traction in certain areas. New forms of health and safety management software are able to be used regardless of internet access and are developed with simple practicality in mind. These emerging forms of risk assessment software can implement the applicable safe work method statement and the intended control measures on a step-by-step basis. Moreover, the completed risk assessment forms are available to be downloaded as a pdf file for future compliance requests.
The construction risk assessment software we’ve developed here at SafeWorkPro is quicker, safer and more compliant. Our example of risk assessment software was developed in consultation with contractors and construction managers but we won’t sit here and try to sell it to you now. Instead, why don’t you just read up on our risk assessment software here and make up your own mind.
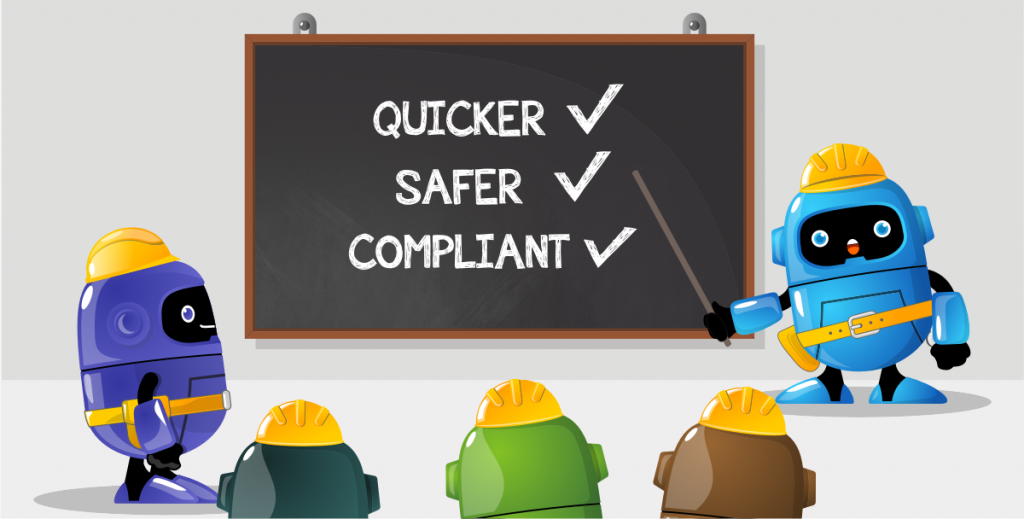
Meet the Regulators: Worksafe Western Australia
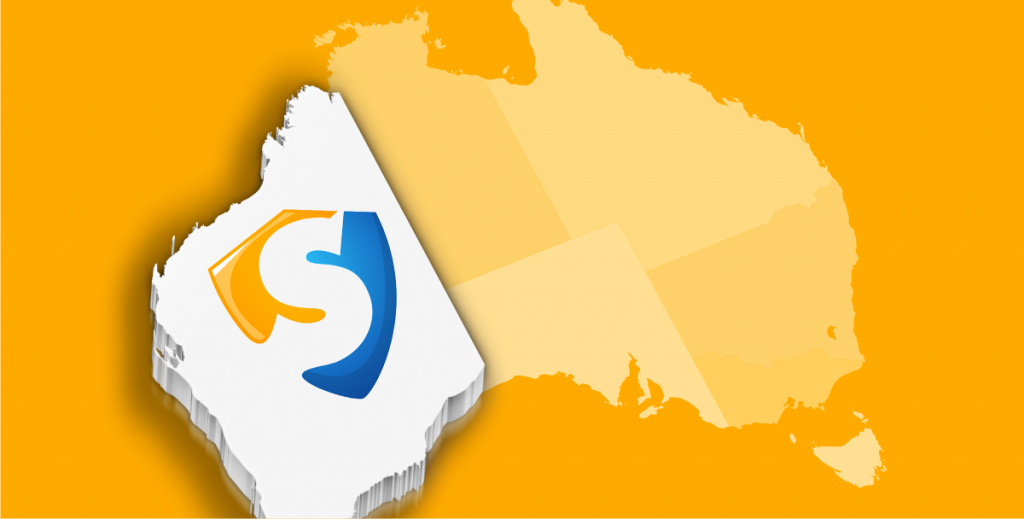
Worksafe Western Australia is a government body responsible for the regulation of the state’s occupational health and safety legislation – specifically the Occupational Safety and Health Act 1984. Worksafe WA is essentially the equivalent of Workcover Western Australia in that its mandate
Responsibilities:
Collaboration with industry, employer and employee groups:
- Influence a commercial environment in Western Australia that promotes best safety practices and empowers businesses to reduce workplace hazard and risk.
- Safeguard the organisational capacity Western Australia Worksafe has to assist the OHS management for all businesses.
Online information and education:
- Provide a digital platform to facilitate the transfer of health and safety information to workers, employers and students.
- The Worksafe Plan Assessment System: this online resource allows organisations to measure and evaluate their OHS record.
Workplace compliance inspections:
- Inspectors use industry specific checklists for a variety of inspection types including reactive, campaign focused, injury and disease focused.
- These inspections are conducted to ensure compliance with OHS codes of practice for Western Australia.
Issue resolution and assistance with risk management:
- Should an OHS dispute occur, Worksafe Western Australia has an issue resolution procedure in place that aims to mitigate differences between employers and employees.
Enforcement in areas of non-compliance:
- Worksafe WA has several enforcement options available including improvement and prohibition notices, verbal or written direction and prosecution.
- Prosecution occurs when notices have failed to prompt compliance, a duty holder repeats an earlier offence, an inspector is prevented from conducting his/her work or there has been a breach of the Occupational Safety and Health Act.
It should be noted that Worksafe Western Australia is not responsible for the regulation of every industry in the state. Although Worksafe WA does regulate most industries, those workplaces involved in mining and petroleum sectors of the economy as well as those covered by the Federal Comcare, are exempt.