How a Simple Process Drives Safety Compliance
Safety management systems have come a long way in the last 250 years. Just think back to workplace conditions during the Industrial Revolution – almost no pay, child labour, very long hours, and extremely dangerous work conditions with exposure to chemicals, accident-prone machinery, and no WHS requirements whatsoever.
But this has changed over the years. Legal reforms and acts were introduced – the Factory Act, the Employer’s Liability Act, and finally, the 1974 Health and Safety at Work Act. This legal document became the foundation for workplace health and safety processes in the UK and the rest of the world. And it led to the increasingly more complex safety processes we have today.
The core purpose of WHS is to keep people safe. Simple. With the increasing complexity of requirements and standards, Business owners, project managers and safety officers alike have to be careful of falling into the trap of using compliance to document requirements like the SWMS as their main measure of WHS compliance. This article looks at why adhering to document requirements is a poor standalone indicator of compliance. We also suggest how a simple safety process drives the success of your WHS compliance.
Documents are Symbols of a Process
Safety isn’t symbolic. It is real and should be treated in the real world, not on a document. Safety management systems do involve documents, but they symbolise a process. For example, a SWMS is a safety planning tool that identifies the risks of high risk construction work and the actions taken to manage those risks. It symbolises the process you are going to take when dealing with the risks and making sure your workplace and its workers are safe from those risks. When it’s under the (judges) hammer, the process symbolised (documented) matters most – not the symbol or the document itself.
Downloading a generic template for your SWMS, JSA, or any other safety document is like taking the symbol without taking the process it represents. And that defeats the whole point of your safety management system and its documents. To comply with WHS requirements, you should be focusing on the processes required to keep your workplace and its workers safe – not just on the documents themselves.
WHS audits look at whether you have followed an effective process that actively reduces the risks in your workplace. They care about if you have actually provided a safe work environment. Not simply whether you have ticked the box of completing a piece of paperwork.
In 2013, The Supreme Court Qld in a case against a QLD construction company for the death of two workers cited:
“work practices focused too much on the work performed onsite and did not pay adequate attention to the dangers presented by the conditions of the site itself”
In other words, not considering risks on the ground, in the real world can have significant impacts when taken to the extremes. Focussing too hard on the details of the tasks to be completed can lead to ignoring all the risks that are actively present
What you focus on matters. And if you want to pass your WHS audit and actually keep your workers safe, then it’s time to focus on the safety management process behind the symbols and documents.
But I still go through a process when filling in a template?
Safety management systems aren’t just about the symbols. They’re about the processes behind them. But you may be wondering – isn’t downloading a generic template still technically a process? Sure. But think about this. What process is more effective at satisfying the Work Health and Safety Act requirement to provide a safe work environment? Is it:
- Find a generic SWMS template on Google, Officeworks or other source
- Complete the boxes provided by the template as best as you can
- Gather up or seek out workers individually and gather signatures
- Store it onsite until the work is done
- Transferring the document to a folder in your office when you are done with the site
Or:
- Identify a the risks onsite, in person
- Build a new SWMS or modify the existing version to cover all task & site-specific risks that are present. Pushed to everyone to sign.
- Monitor how measures are being implemented while work is being completed with real time automated risk rating notifications
- Review by anyone relevant once the work has been completed
- Automatic document storage once complete for any future audits, follow-ups, or learning
From a legal standpoint, the second option is better,
The very purpose of developing a SWMS is to ensure that employers and workers have taken the time to identify the high-risk tasks to be done on site. And then, it is to develop measures to manage these risks and tasks in the context of the work being done. The very nature of a SWMS is that it is specific. It is created specifically in response to a specific site, specific tasks, and specific risks. A generic templated SWMS will not meet the intention behind WHS requirements. Instead, it will defeat the real power of the SWMS and even take away from your safety management.
As WorkSafe Victoria explains, “our concern is not what is written but what actually happens”. A generic SWMS is a symbol of safety that only provides guidance. To focus on the process and comply with WHS requirements, your SWMS and other safety documents need to be customised. It is the second process that is more likely to pass a WHS audit because it demonstrates an active approach to creating a safe work environment. And it is the first process that will get a much more severe punishment when a safety incident does happen, even though both processes are represented by the same type of document.
How to Prioritize the Process
The simplest way to boost the effectiveness of your safety process is to use a digital safety platform like SafeWorkPro. While you can do your safety management physically or digitally, doing it digitally is what will make the difference. Why?
Safety management software simplifies your safety management. Turning a complex process into a simple, easy to understand workflow that allows for an easier way to assess, mitigate, monitor and review workplace risks of all nature. It makes sure that your safety management system is customised, comprehensive, and lets you focus on the process. Leave the document creation, distribution and storage to the software. With safety management software, you can seamlessly customise, prioritise, and ensure your safety management system and its processes exceed WHS regulations.
SafeWorkPro is the Australian safety management software that can make sure your workplace prioritises the process over the symbols.
- Customise your SWMS, JSA, or other safety documents specifically to your worksite using our flexible document builder
- Make sure your specific workplace risks are managed and your workers are safe
- Ensure your company truly complies with WHS requirements
Do all of this seamlessly and in one place with the SafeWorkPro platform. Click the button below to find out more.
More From The SafeWorkPro Blog
Risk assessments: How to keep work safety switched on in an offline environment
Out of sight, out of mind
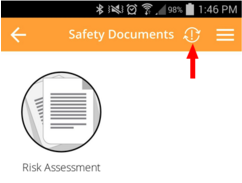
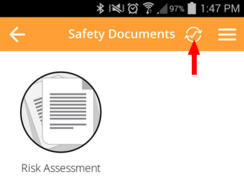
Freedom to Move
Many occupations require work to be undergone in remote regions, often out of reach of internet connectivity. At SafeWorkPro we understand these areas are the ones that require the most meticulous safety procedures, risk assessment document and emergency planning. Therefore we have ensured our applications functionality still runs smoothly when you get that annoying no signal sign on your mobile device. You can still take photos, create documents and assess risk no matter where your work day takes you.
So if you never want to lose access to safety again, sign-up to a trial of SafeWorkPro.
Why Buy Risk Assessments?
If you’re running a construction business or managing a worksite then you know the risk assessment process inside and out. You’ll know how to implement a safe work method statement (SWMS), rate a risk assessment matrix and complete a job safety analysis – all just part of remaining compliant with health and safety rules. All this paperwork seems like a hassle (and it is) so why don’t businesses involved in high risk construction work just buy risk assessments?
There’s two answers to this question. Firstly, businesses don’t just get up and buy risk assessments because free risk assessment software alternatives already exist. Otherwise called job safety analysis software, construction safety software or health and safety management software, these digital alternatives to paperwork are known to cut costs and improve productivity. So if you’re a manager or business owner, you’d know it makes more long-term business sense to invest in risk assessment software rather than buy the paperwork (esp SWMS).
The second reason why smart businesses don’t just buy risk assessments is because risk assessments in the workplace have a nasty habit of becoming obsolete as new hazards emerge. To remain compliant with OHS laws, risk assessments must be reviewed and updated as soon as working conditions change and more risks become apparent. So there’s little point buying an expensive SWMS document only to see it become obsolete once a worker finds some rusty nails sticking out of a floorboard.
With the option of risk assessment software free download available, the key lesson here is not to buy risk assessments. With so many alternatives out there and with the limitations of paper-based risk assessments holding back your ability to improve productivity, spending your hard earned cash on a pile of paper work is a waste of resources. You can learn more about these alternative including SafeWorkPro’s risk assessment software here.
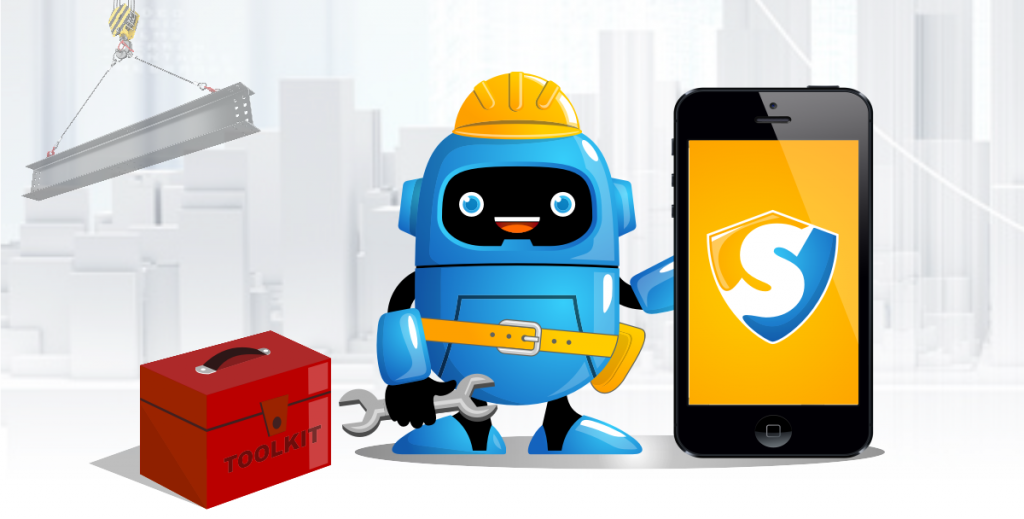
Types of Risk in Construction
Health risks at work can range from catching a common cold off co-workers to suffering a serious injury. These risks however, are far more prominent in the construction industry, which saw 17 workplace deaths in 2013*. This is a stark figure, especially for a developed and modern country like Australia. Nonetheless the number of Australian worker injuries and fatalities is a solemn reminder of the inherent dangers involved in high risk construction work.
The central role risk assessments play in preventing injury and fatalities is more evident than ever but there is more to the risk assessment process than paperwork and red tape. According to section 291 of the Work Health and Safety Act, there are 18 types of high risk work. These include construction activities which:
(a) involves a risk of a person falling more than 2 metres; or
(b) is carried out on a telecommunication tower; or
(c) involves demolition of an element of a structure that is load‑bearing or otherwise related to the physical integrity of the structure; or
(d) involves, or is likely to involve, the disturbance of asbestos; or
(e) involves structural alterations or repairs that require temporary support to prevent collapse; or
(f) is carried out in or near a confined space; or
(g) is carried out in or near:
(i) a shaft or trench with an excavated depth greater than 1·5 metres; or
(ii) a tunnel; or
(h) involves the use of explosives; or
(i) is carried out on or near pressurised gas distribution mains or piping; or
(j) is carried out on or near chemical, fuel or refrigerant lines; or
(k) is carried out on or near energised electrical installations or services; or
(l) is carried out in an area that may have a contaminated or flammable atmosphere; or
(m) involves tilt‑up or precast concrete; or
(n) is carried out on, in or adjacent to a road, railway, shipping lane or other traffic corridor that is in use by traffic other than pedestrians; or
(o) is carried out in an area at a workplace in which there is any movement of powered mobile plant; or
(p) is carried out in an area in which there are artificial extremes of temperature; or
(q) is carried out in or near water or other liquid that involves a risk of drowning; or
(r) involves diving work
In many of the above cases, contractors and workers are required to gain special licences and risk assessment training before conducting any work. This is to ensure that those engaging in high risk construction work are aware of the risks involved, trained to deal with these risks and properly accredited. For more information, head to Safe Work Australia’s licensing page.
*Source: Safe Work Australia, Worker fatalities.