3 Signs Safety Software Might Be The Solution For You
Safety software is a relatively new solution to an old problem. Have you ever thought to yourself, there has got to be a better way to stay complaint with safety regulations? Do you ever get frustrated that you have to fill out so many assessments and statements on paper. Do you find yourself missing things in your assessments because you are worried that it’s not in the right format?
These are just some of the frustrations that come with the process of staying compliant with safety regulations. It can have significant effects on your safety culture if you find the process of safety too difficult. If you have ever ran into any of the above, it might be time to consider finding a solution before it becomes too much of a headache that safety goes out the window and all your effort is spent just to be compliant.
In this article we will cover in depth 3 signs that it might be time to consider utilizing safety software before your safety is ignored for compliance.
You’re worried about compliance incase of an incident
Running a business is no easy task. It’s like juggling 10 things at once. When things are going well, it’s a great feeling. But it only takes one slip up or incident to cause everything to come crumbling down. The stress and anxiety of a WHS incident happening in your business is enough to keep anyone up at night. On top of that, if you know you might get slapped with a fine after the incident you’ll always be stressed or worse, you’ll delay reporting an incident. This can lead to huge fines and even jail time. No one wants that.
Safety compliance in the modern day is no simple task. There are a lot of regulations and legislation that you must adhere to in your day to day business. This can become quite a headache and adds to the stress of making sure you have ticked all the boxes. Or worse, leads you to ignoring your requirements and hoping that an incident doesn’t occur. As we have covered in a previous article, incidents happen to even the best of employers who are proactive with safety, its simply the reality of probability. If there is a chance, eventually it will happen.
Ask yourself this. If there was an incident at your workplace tomorrow and it lead to an inspection, would you be confident you would pass? Have you got a solid and refined risk assessment process in place to identify, assess and control risks in your workplace?
If the answer is not a confident yes then it might be time to look at solutions. Safety software like our platform SafeWorkPro allows you to focus on your process more while making the document compliance side of things a worry of the past. While SafeWorkPro won’t solve all of your safety worries, it will help you be more effective with your time so you can spend less time filling out forms and more time focusing on the actions that lead to a safer workplace. We have talked about how your process is more important than your documents in a previous article. In the eyes of the law, the concern is about what you actually do to keep people safe.
If you want to spend more time on safety and less time on the books, then safety software might be the solution for you.
Safety software makes documentation simple and easy
How long does it take you to complete a risk assessment from start to finish? What about a SWMS? Do you find it difficult to complete documents because of all the back and forth that is required between the site, office and in between your workers? If your documentation process is top notch and you have no issues with filling out lengthy paper documents then this might not apply to you. But for those that get frustrated with how much time away from work they have to take to complete documents, this one might be for you.
When the bottle neck for starting a job is the paperwork you need to complete for safety compliance it can become frustrating. It can sometimes feel like too much time is being wasted on paperwork when you could be working. This can lead to rushing through it which defeats its purpose. It also means that you are more likely to skip the processes that really matter to keep people safe.
If you are on a site that needs a SWMS and something changes that requires you to re-evaluate your SWMS, the process starts again and the tools are down until it is done. With safety software, the process of completing documentation is significantly easier. In principle, it is the same but in practice you’re saving time that would otherwise be spent filling a document and running around to get it signed. SafeWorkPro’s simple form based builder allows you to build custom documents which are super simple for your workers to complete on site when needed.
Save the hassle of the back and forth trying to get your documents read and signed by those on site. Have workers fill and sign documents from anywhere on site and have them submitted to the cloud for you to review from any location. SafeWorkPro even lets you get notifications when certain actions happen like a risk rating on a risk assessment matrix being too high or an incident is submitted. SafeWorkPro can help you save time on compliance and let’s you focus on what you do best.
Safety software helps you find old documents quick
Ask yourself this, can you find your risk assessment or SWMS from a job 2 years ago? If you were audited, could you produce it? This is something that isn’t obvious until it is an issue and by then it’s too late. How much of an impact on your day to day operations would a surprise audit have? Would you need to go digging through the back office folders to find the documents required? What a headache!
Even while you are on site, your documents like a SWMS need to be available for everyone to see. While they are there, they are likely to get damaged or degraded by weather. Sometimes, by the time they get stored for safe keeping they are almost falling apart.
With the safety of cloud document storage, SafeWorkPro can store all of your important documents online forever. With all of your documents in one place and neatly organized it’s super simple to find the documents you need, even if they are from years ago. Our software also makes audits quick and easy with next to no disruption in your operations. Export all of the data from your SafeWorkPro site for review without having to spend hours digging through folders, photocopying and physically delivering documents.
Conclusion
If any part of this article resonates with you, it might be time to consider trying out a better solution to using a manual safety process. Beyond just the convenience, SafeWorkPro can help you focus your time on the actions that truly make people safe, not just the actions that make you compliant. At the end of the day, that is what you will be judged on if you have an audit or investigation. Documentation is required of course, but that is simple the surface level when it comes to safety.
If you want to learn more about how SafeWorkPro could help you in simplifying your WHS, reach out to our friendly expert staff for a free, no obligation live demo.
Working in Confined Spaces Risk Assessment
Whether you work in an office or under the sun, sometimes everyone feels like they’re working in a tiny, unescapable box. When it comes to high risk construction work however, there is a specific meaning for working in confined spaces. This affects the many different factors a confined spaces risk assessment must take into account when conducting hazard management.
Regulation 5 of Australia’s Work Health and Safety Regulation defines a confined space based on to the hazards associated with it. Under this definition and under the codes of practice outlined by Safe Work Australia, a confined space means an enclosed or partially enclosed space that:
o is not designed or intended primarily to be occupied by a person; and
o is, or is designed or intended to be, at normal atmospheric pressure while any person is in the space; and
o is or is likely to be a risk to health and safety from:
- an atmosphere that does not have a safe oxygen level, or contains contaminants, including airborne gases, vapours and dusts, that may cause injury
- fire or explosion, or harmful contaminants
- engulfment.
- examples may include vats, tanks, pits, pipes, ducts, flues, chimneys, silos, containers, pressure vessels, underground sewers, wet or dry wells, shafts, trenches, tunnels
Many of the generic risks involved with working in confined spaces include:
o loss of consciousness, impairment, injury or death due to the immediate effects of:
- airborne contaminants
- fire or explosion from the ignition of flammable contaminants
- difficulty rescuing and treating an injured or unconscious person
o asphyxiation resulting from oxygen deficiency or immersion in a free-flowing material such as grain, sand, fertiliser, water or other liquids.
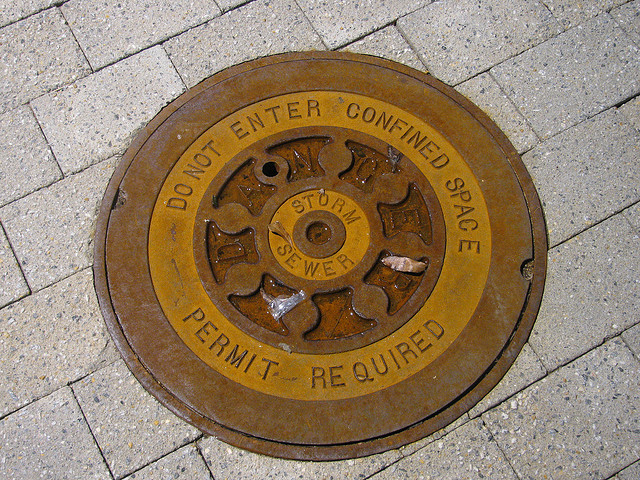
An effective and compliant confined space risk assessment example will take notice of these generic but identifiable hazards:
- Restricted entry or exit
- Presence of harmful airborne contaminants
- Unsafe oxygen levels caused when oxygen in the atmosphere is:
- Fire and explosion
- Unstable substances that risk engulfment
- Uncontrolled introduction of substances
- Contact with biological agents
- Exposure to mechanical hazards
- Contact with electrical hazards
- Skin contact with hazardous substances (this will require a hazardous substances risk assessment)
- Noise
- Manual tasks
- Radiation
- Environmental hazards
For more details on these hazards and the related risk control measures, read the SafeWorkPro Blog.
Control Measures for Confined Space Safe Work Procedure
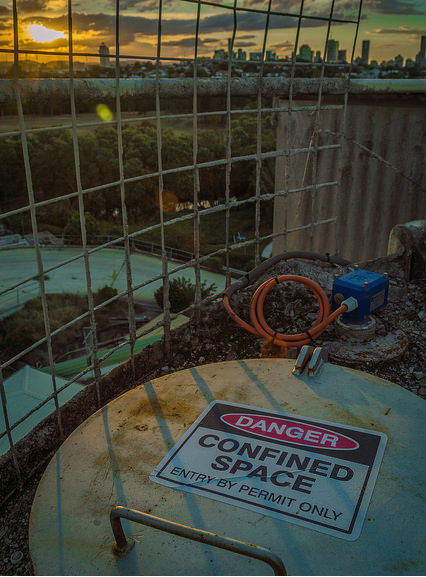
In previous articles on the SafeWorkPro Blog, we’ve looked at the risks and hazards of working in confined spaces. But what good is a risk if there no control measures?
Below is an extensive list taken the codes of practiceby Safe Work Australia, that outline the various control measures available to construction workers and PCBU’s involved in high risk construction work. Before conducting work in a confined space, it is strongly recommended that all duty holders consult this list, and more importantly, the relevant codes of practice. The control measures outlined by Safe Work Australia include:
Entry permit: A PCBU must not allow or direct a worker to enter a confined space to carry out work unless the person has issued a confined space entry permit for the work. A space entry permit must be completed (in writing) by a competent person and specify:
- specify the confined space to which the permit relates record the names of persons permitted to enter the confined space and the period of time that the work will be carried out
- set out risk control measures based on the risk assessment, and contain space for an acknowledgement that work in the confined space has been completed and all persons have left the space.
Isolation: All potentially hazardous services should be isolated prior to any person entering the confined space. These services may include piping, vents, drains, conveyors, service pipes, machinery, plant, electrical equipment or fire protection equipment.
- Physically tag, lock, close or blank hazardous service
- Removal of valve, spool piece or expansion joint in piping that leads to confined space
- Remove energy source to any agitator, fans or other moving parts in a confined space (if energy source cannot be removed consider choking, wedging, chaining or removing any moving parts)
- Reduce any device with stored energy including hydraulic, pneumatic, electrical, chemical, mechanical, thermal or other types of energy, to a condition of zero energy
Atmosphere conditions: a safe atmosphere has a safe oxygen level, is free of airborne contaminants o has concentrations below their allowable exposure standard, has concentrations of flammable gas or vapour below 5% of its LEL. Control methods include:
- Purging: use an inert gas, such as nitrogen, to clear flammable gases or vapours out of the confined space. Following purging, the space should be ventilated with sufficiently fresh air and any removed contaminants should be expelled to a location that presents no further risk. Before conducting work in the confined space, atmospheric testing should be carried out
- Ventilation: may be necessary to establish and maintain a safe atmosphere and temperature for as long as work is conducted in the confined space
- Natural ventilation: only if the confined space has sufficient openings and the source of fresh is not contaminated by any exhaust or other pollutants
- Mechanical ventilation: use local exhaust ventilation (LEV) for localised contaminant generation (eg extraction of welding fumes). LEV should be monitored during operation and have controls clearly identified, tagged and protected
- Dilution ventilation: air must be introduced in way that ensures effective circulation through the confined space with openings, contamination level and area layout put into consideration
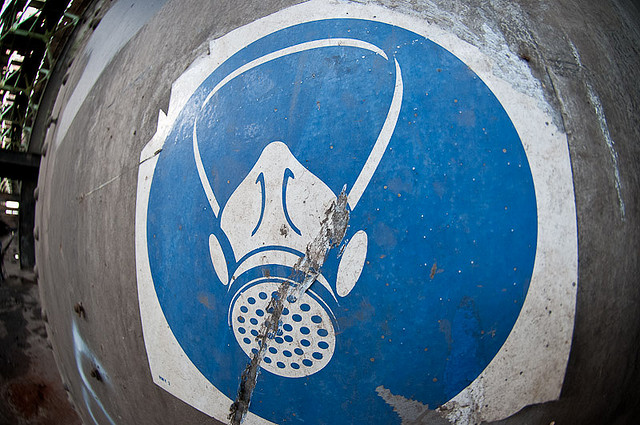
Respiratory protective equipment (RPE): if it is not reasonably practicable to ensure a safe oxygen level, remove the confined space of contaminants or when there is an unknown concentration of a hazardous substance is present, then respiratory protective equipment must be worn.
- AS/NZS 1715: Selection, use and maintenance of RPE
Safety monitoring: a standby person must be assigned to the vicinity before a worker enters a confined space to continuously monitor the wellbeing of those inside the space.
- The standby person should be aware and understand the risks inside the confined space and be able to recognise signs and symptoms of distress that workers in confined space may experience (reg 69)
- The standby person should remain outside the confined space and do not other work that impedes their monitoring duties
- A required rescue and safety equipment should be available to standby person
- The standby person should have the authority to order an evacuation and never enter the space to attempt a rescue
What is Job Safety Analysis?
Did you know that panthers and leopards are the same animal? No jokes. Only their fur coats are different, everything else is the same. Believe it or not, job safety analysis forms are similar (minus the claws, teeth, agility and general awesomeness).
Otherwise known as a risk assessment or a job task analysis, job safety analyses (JSA for short) aim to identify hazards and implement measures that will control or at least minimise the risk involved in construction work. Job safety analysis forms come in a variety of types but all share the common traits. The below job safety analysis template comes from the Victorian WorkCover Authority and gives you an idea of correct layout.

As you can see from the above job safety analysis worksheet, there are four parts to a good JSA template.
1: Classify the tasks: along with everyone involved in the high risk construction work, write down each of the steps that make up the job.
2: Hazard and risk identification: besides each step, write down what injuries or health threats are involved.
3: Document the control measures: next to each hazard assessment, specify what control measures will be used to eliminate or reduce the risk of injury or ill health.
4: Distribute responsibility: outline who is responsible for the implementation of each control measure.
One more point that you’ll need to remember. If an incident does occur in the workplace that results in injury or ill health, your job safety analysis could very well be used in court proceedings. This means every duty holder must sign off and review the job safety analysis worksheet should safety conditions change.
So it’s all pretty similar stuff. Panther or leopard? Risk assessment or job safety analysis? Same things, different names.
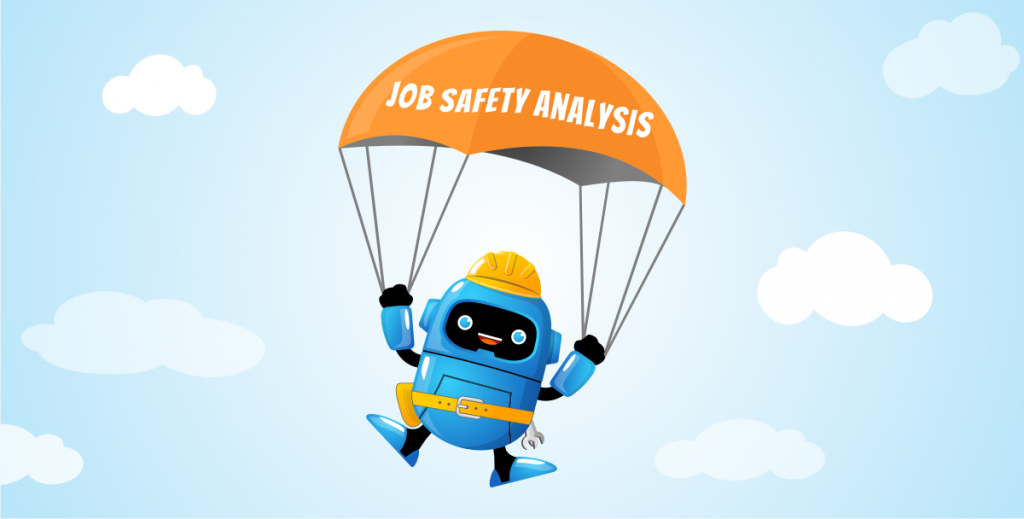