3 Signs Safety Software Might Be The Solution For You
Safety software is a relatively new solution to an old problem. Have you ever thought to yourself, there has got to be a better way to stay complaint with safety regulations? Do you ever get frustrated that you have to fill out so many assessments and statements on paper. Do you find yourself missing things in your assessments because you are worried that it’s not in the right format?
These are just some of the frustrations that come with the process of staying compliant with safety regulations. It can have significant effects on your safety culture if you find the process of safety too difficult. If you have ever ran into any of the above, it might be time to consider finding a solution before it becomes too much of a headache that safety goes out the window and all your effort is spent just to be compliant.
In this article we will cover in depth 3 signs that it might be time to consider utilizing safety software before your safety is ignored for compliance.
You’re worried about compliance incase of an incident
Running a business is no easy task. It’s like juggling 10 things at once. When things are going well, it’s a great feeling. But it only takes one slip up or incident to cause everything to come crumbling down. The stress and anxiety of a WHS incident happening in your business is enough to keep anyone up at night. On top of that, if you know you might get slapped with a fine after the incident you’ll always be stressed or worse, you’ll delay reporting an incident. This can lead to huge fines and even jail time. No one wants that.
Safety compliance in the modern day is no simple task. There are a lot of regulations and legislation that you must adhere to in your day to day business. This can become quite a headache and adds to the stress of making sure you have ticked all the boxes. Or worse, leads you to ignoring your requirements and hoping that an incident doesn’t occur. As we have covered in a previous article, incidents happen to even the best of employers who are proactive with safety, its simply the reality of probability. If there is a chance, eventually it will happen.
Ask yourself this. If there was an incident at your workplace tomorrow and it lead to an inspection, would you be confident you would pass? Have you got a solid and refined risk assessment process in place to identify, assess and control risks in your workplace?
If the answer is not a confident yes then it might be time to look at solutions. Safety software like our platform SafeWorkPro allows you to focus on your process more while making the document compliance side of things a worry of the past. While SafeWorkPro won’t solve all of your safety worries, it will help you be more effective with your time so you can spend less time filling out forms and more time focusing on the actions that lead to a safer workplace. We have talked about how your process is more important than your documents in a previous article. In the eyes of the law, the concern is about what you actually do to keep people safe.
If you want to spend more time on safety and less time on the books, then safety software might be the solution for you.
Safety software makes documentation simple and easy
How long does it take you to complete a risk assessment from start to finish? What about a SWMS? Do you find it difficult to complete documents because of all the back and forth that is required between the site, office and in between your workers? If your documentation process is top notch and you have no issues with filling out lengthy paper documents then this might not apply to you. But for those that get frustrated with how much time away from work they have to take to complete documents, this one might be for you.
When the bottle neck for starting a job is the paperwork you need to complete for safety compliance it can become frustrating. It can sometimes feel like too much time is being wasted on paperwork when you could be working. This can lead to rushing through it which defeats its purpose. It also means that you are more likely to skip the processes that really matter to keep people safe.
If you are on a site that needs a SWMS and something changes that requires you to re-evaluate your SWMS, the process starts again and the tools are down until it is done. With safety software, the process of completing documentation is significantly easier. In principle, it is the same but in practice you’re saving time that would otherwise be spent filling a document and running around to get it signed. SafeWorkPro’s simple form based builder allows you to build custom documents which are super simple for your workers to complete on site when needed.
Save the hassle of the back and forth trying to get your documents read and signed by those on site. Have workers fill and sign documents from anywhere on site and have them submitted to the cloud for you to review from any location. SafeWorkPro even lets you get notifications when certain actions happen like a risk rating on a risk assessment matrix being too high or an incident is submitted. SafeWorkPro can help you save time on compliance and let’s you focus on what you do best.
Safety software helps you find old documents quick
Ask yourself this, can you find your risk assessment or SWMS from a job 2 years ago? If you were audited, could you produce it? This is something that isn’t obvious until it is an issue and by then it’s too late. How much of an impact on your day to day operations would a surprise audit have? Would you need to go digging through the back office folders to find the documents required? What a headache!
Even while you are on site, your documents like a SWMS need to be available for everyone to see. While they are there, they are likely to get damaged or degraded by weather. Sometimes, by the time they get stored for safe keeping they are almost falling apart.
With the safety of cloud document storage, SafeWorkPro can store all of your important documents online forever. With all of your documents in one place and neatly organized it’s super simple to find the documents you need, even if they are from years ago. Our software also makes audits quick and easy with next to no disruption in your operations. Export all of the data from your SafeWorkPro site for review without having to spend hours digging through folders, photocopying and physically delivering documents.
Conclusion
If any part of this article resonates with you, it might be time to consider trying out a better solution to using a manual safety process. Beyond just the convenience, SafeWorkPro can help you focus your time on the actions that truly make people safe, not just the actions that make you compliant. At the end of the day, that is what you will be judged on if you have an audit or investigation. Documentation is required of course, but that is simple the surface level when it comes to safety.
If you want to learn more about how SafeWorkPro could help you in simplifying your WHS, reach out to our friendly expert staff for a free, no obligation live demo.
How To Identify Asbestos
A key aspect of a safe and complete asbestos risk assessment is the inclusion of a hazardous substance risk assessment form. This is not something that should be taken lightly as asbestos in homes is a real risk in any property built before 1990. Therefore knowing how to identify asbestos is a critical step in any type of asbestos training.
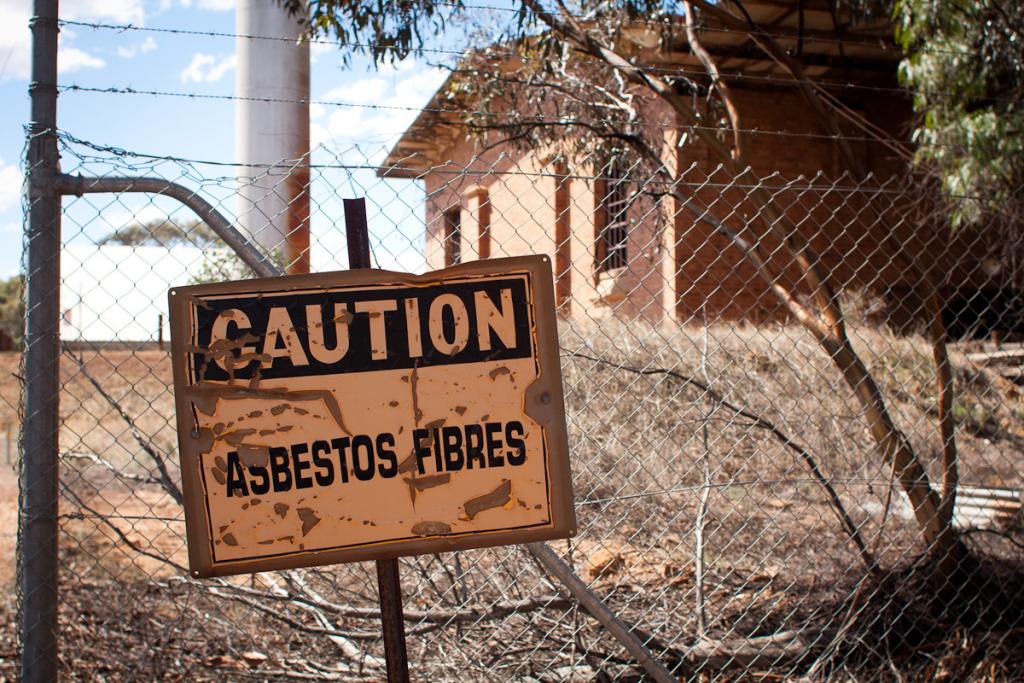
But this can be an expensive option. If you wish to test any material you suspect of containing asbestos, you can contact the National Association of testing Authorities for an independent evaluation. With over 3000 asbestos containing products used in construction prior to 1990, professional consultation and testing is the safest option for the identification of this highly hazardous material. But there are several common characteristics of asbestos containing materials.
Warning signs: look for any warning signs or labels that indicate the existence of asbestos.
Age: any property built before the late 1980’s could contain asbestos. Consult with local authorities, the structure’s builder, previous owners and neighbours.
Fasteners and joints: check the battens used to to cover the joints between sheets of asbestos containing materials like AC sheeting. Any broken battens, gaps in joiners or loose nails, can indicate the presence of asbestos.
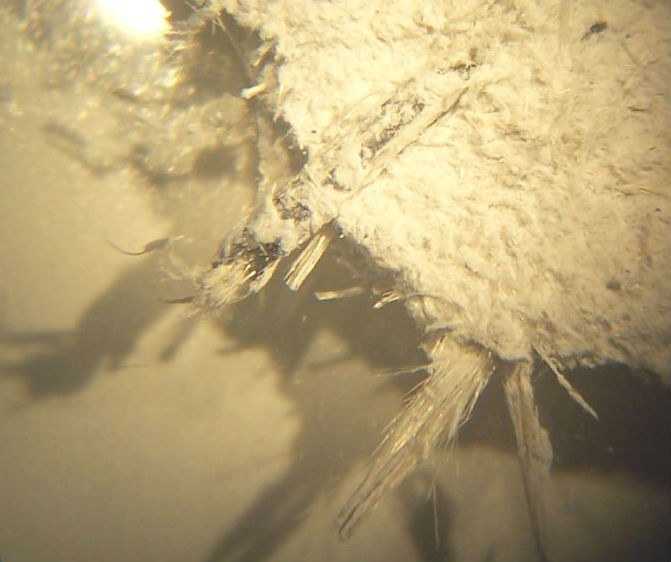
Close inspection: if you have a digital camera with a macro mode function, use it to take a close up photo of the material. Asbestos fibres are microscopic but the strands that are made up of these fibres can often be found clumped together (see left image for example). Note: never break the material apart to check as it could release asbestos fibres into the immediate area.
It must be noted that these are initial steps and cannot guarantee the total identification of all asbestos materials. For that, an accredited asbestos specialist will need to be engaged.
Hazardous Substances Risk Assessment
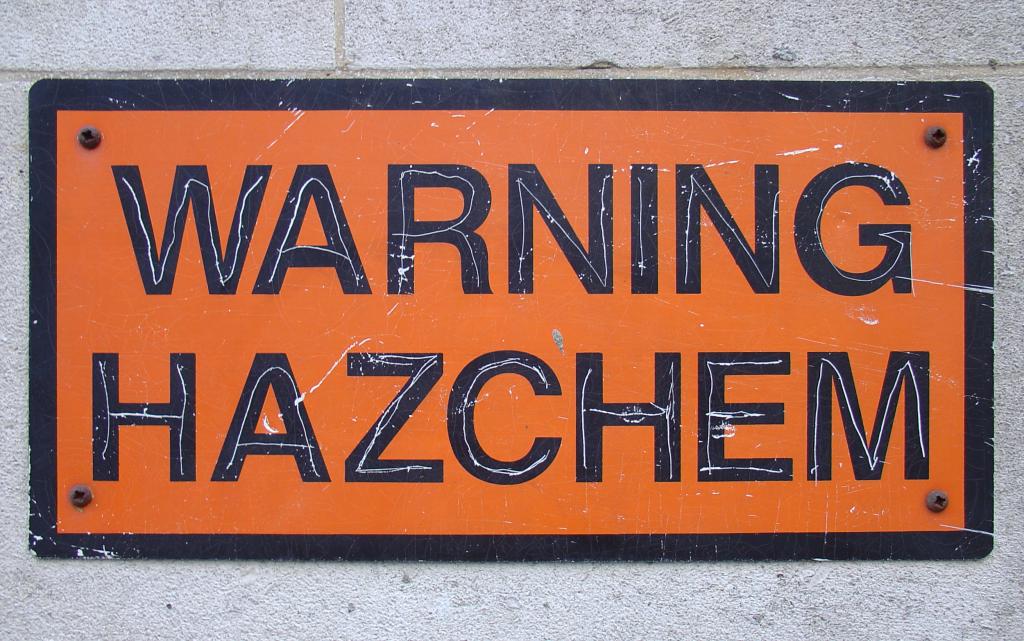
Managing risk can be a complicated task especially when looking at a risk assessment for chemicals. This is a whole new ball game for risk management consultants and the harmonisation of regulatory frameworks don’t make this any clearer. The problem hazardous substances (or chemicals) have in high risk construction work is that the
ordinary worker won’t know how to identify the specific elements and compounds that make a substance hazardous, nor have an in depth understanding of the appropriate control measures.
To soften the inherent risks involved to the maximum degree possible, Safe Work Australia and the relevant state regulators require the importers and manufacturers of hazardous chemicals to provide a Safety Data Sheet (SDS) to the people or organisations using their product. The SDS provides the PCBU and workers with information on the dangers involved with a substance, the controls methods and forms of treatment should an incident occur. All this information is vital in the writing of a compliant hazardous substances risk assessment.
A hazardous substance risk assessment form differs from other risk assessment in construction in that it must include information such as the health effects, signal words, precautionary details, control measures and recommended protective equipment that are outlined in the SDS. An example of this in a risk assessment form is below.
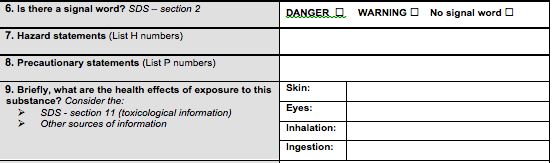
That all being said, the underlying elements of a compliant risk assessment for construction, including the hierarchy of control measures, remains largely the same. Hazard and risk identification, the implementation of control measures, the duty of care and review process, all remain core components of a hazardous substance risk assessment.
For more information, read Safe Work Australia’s guide for the preparation of Safety Data Sheets.
The Codes of a Chemical Risk Assessment
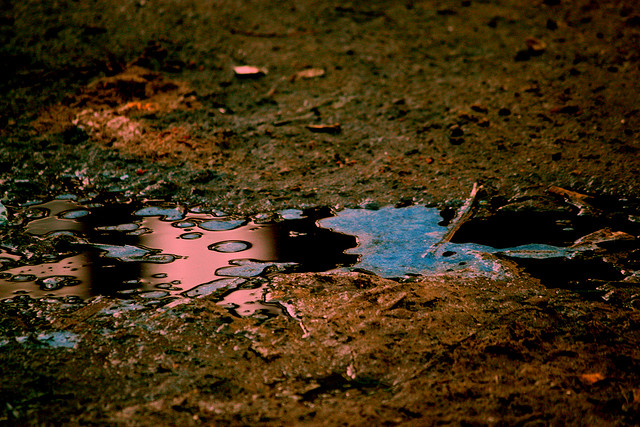
Chemistry is complicated stuff and a risk assessment for chemicals is no different. The range of hazardous chemicals used in the Australian construction industry is only overshadowed by the number of risks associated with them. A chemical risk assessment must take all of these inherent dangers into account but understanding every substance or chemical, along with the
associated risks and hazards, is not a reasonably practicable option for most construction businesses.
Therefore the Safe Work Australia provides a list of codes used in Safety Data Sheets to explain the various hazards and risks associated with hazardous chemicals. This resource is provides both construction workers and managers with quick and easy to understand explanations of each chemical code and the related hazard.
Your hazardous substances risk assessment should then include these codes in the risk identification process when applicable. The benefit of including this in your chemical risk assessment form is that it not only improves how workers understand the risk involved with hazardous chemical but it also displays an attempt on behalf of the PCBU to ensure a safe working environment.
To improve your chemical risk assessments along with your workplace health and safety, you can access a full list of the codes here.